Optimization of a production facility
Optimization of production at a manufacturing plant is a topic covered in hundreds of books, courses, and training. Plants have existed since the Industrial Revolution, yet many principles and best practices are universal. However, due to the nature of their operations, there are even more situations when businesses go against standard practices. This article will cover some principles that can be considered universal and thus applicable to most industries and manufacturing facilities.
"How is it going, bud"?
One of the most common pieces of advice you might hear is proper communication with the employees. Walk from one workstation to another and ask employees what is slowing them down or making their work inefficient. Then, start solving your employees' problems, and in a few months (or years), you will have a perfectly run facility. It sounds like a solid plan. However, it rarely works at a facility that employs more than a few dozen people. However, this approach can still be implemented as part of other improvements. It is about the Kaizen principle or incremental improvements. Even small changes result in a significant outcome after a specific time.
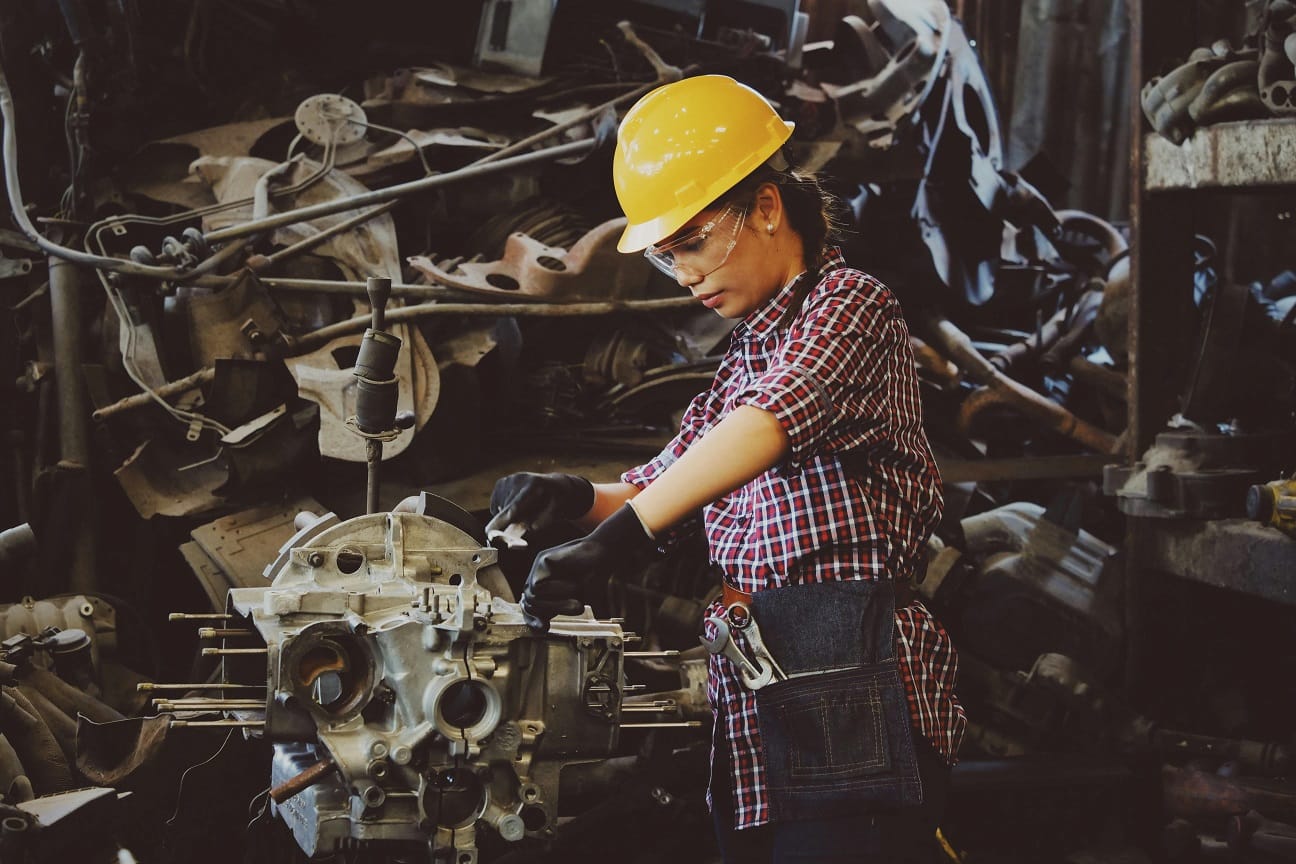
Let's say the office's front end (or back end, depending on the perspective) is done, and an order is sent to a factory. Imagine that only a sketch or description of a part is available, and now it is up to a drafter to prepare a drawing that can be shared with the client for their review or approval. Unless it is a brand-new facility and every single employee is new, there is usually a "standard" way of doing things. However, using SoP, i.e., standard operating procedures, is the best way to minimize errors.
Writing those procedures is always time-consuming, but they solve many potential issues with the inconsistency of a specific process outcome. A drafter must know what format a drawing should be prepared, what kind of checks it should undergo, and so on. This is also a perfect opportunity to implement the first quality control (QC) checks. The earlier you find mistakes in your process, the less they will cost the company. If you wait until the whole batch of products is produced to conduct the QC checks, it will be too late and result in extreme rework volumes. This also helps eliminate the Mudas of Lean manufacturing - Muda of Waste.
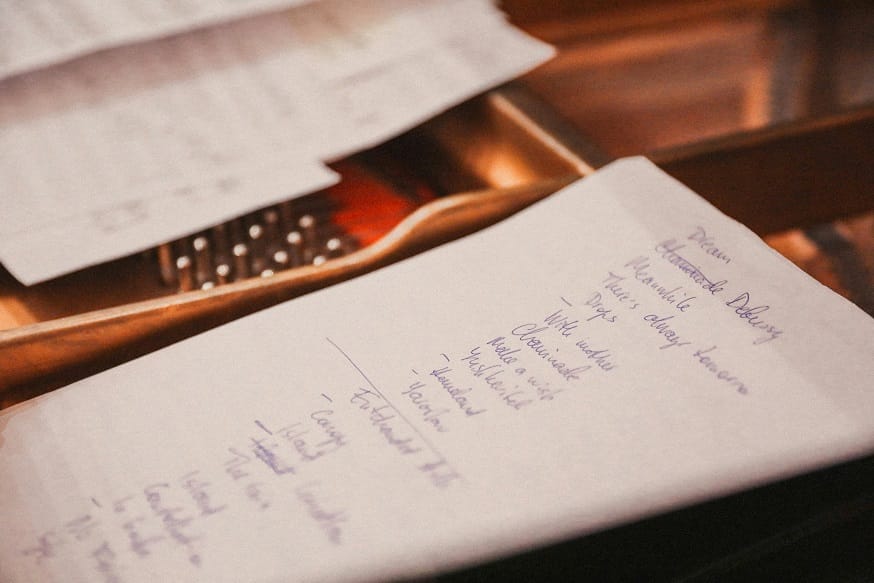
"What are you working on"?
The first step is also great for putting it onto a Kanban board. This is another Japanese technique used in project management, operations and manufacturing. Overall, a Kanban board can be physical or digital, depending on the working environment, but Agile proponents always prefer a low-tech, high-touch approach. A Kanban board is essentially a table with various columns, usually named design, QC, fabrication, etc. There are a few advantages of using the Kanban approach, such as visualizing a workflow and controlling work in progress.
If a department or workstation's workflow is visualized and visible to everyone, it creates transparency and builds trust, which is beneficial for overall productivity. Limiting work in progress makes it apparent what kind of bottlenecks a specific process has. It helps allocate resources accordingly and tackle two other types of Waste—overproduction and waiting. In the case of Kanban, the work-in-progress limit is the number of cards on the board (or tasks) allowed in a single column.
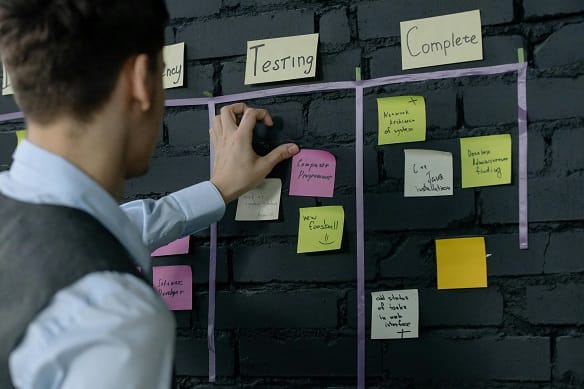
There is a very good reason behind this approach. Imagine that a structural engineer needs to review a design or the account manager needs to check the costs. Those specialists or departments can only work on a few projects at a time without jeopardizing the quality of their work. Since those tasks are displayed on a Kanban board, having a visual reference helps all employees track their progress.
Visual Cards and Pull System
Kanban cards are visually designed and color-coded to show the part number, location, quantity, and special instructions. They follow the production flow from station to station, ensuring that each task is only pulled to the next stage when it is ready. For example, if Quality Control is at its WIP limit, the QC team won't pull the new item until there is room. This helps balance the workflow and prevents idle time or excess inventory buildup. This pull system limits overproduction and reduces waste. For instance, if an engine component is needed at a workstation, a Kanban card will move from assembly to procurement, triggering a request for parts. Based on real-time demand, this signal tells upstream processes when to produce more parts.
Kanban also helps establish a pull system. Traditionally, tasks are assigned to employees, and this is called a push system. Conversely, Kanban promotes the polar opposite approach—a pull system when employees pick tasks from a backlog. In manufacturing, a pull system is implemented in a similar way.
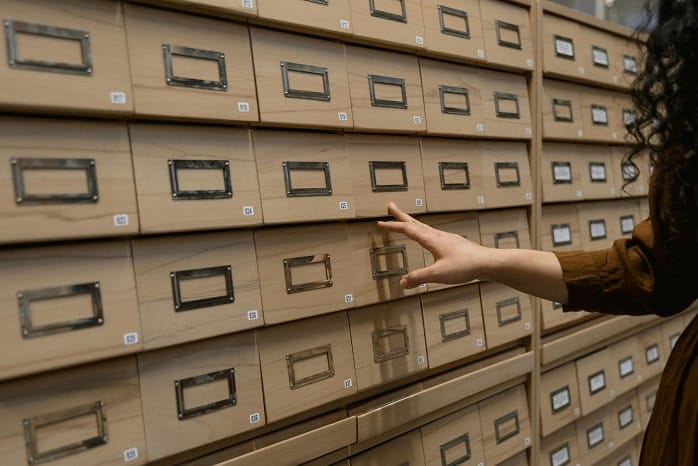
Two-Bin System for Inventory Control
Toyota, which is not always the inventor, but a great adapter to optimization methods, uses a two bin-system for inventory control. Each bin is stocked with the necessary parts to keep production going. When one bin runs empty, a Kanban card attached to the bin signals to replenish that part. The empty bin goes back to the supplier or storage area with the Kanban card to signal the need for refilling, ensuring the production line has what it needs without excess stock. Sometimes, there is no Kanban card, but some means for visual indication that a bin is empty. It could be a light that turns on or off, a visual marking on the floor, or any other method suitable for the particular fabrication setup.
Value Stream Mapping (VSM)
Kanban is a valuable tool for optimizing many processes at a fabrication facility. Another helpful technique, value stream mapping, helps to identify bottlenecks and potential avenues for improvement. This method visualizes, analyzes, and improves the flow of materials and information/documents required to deliver a product or service to a customer.
In order to create a value stream map, you need to choose a specific product or process. Then, you must start including all steps, material, or information flow. You usually start with the first step and then track cycle times, lead times, and other applicable key metrics. It is possible to analyze where delays (bottlenecks) and non-value-adding activities occur. Based on that information, you can start implementing an improvement plan.
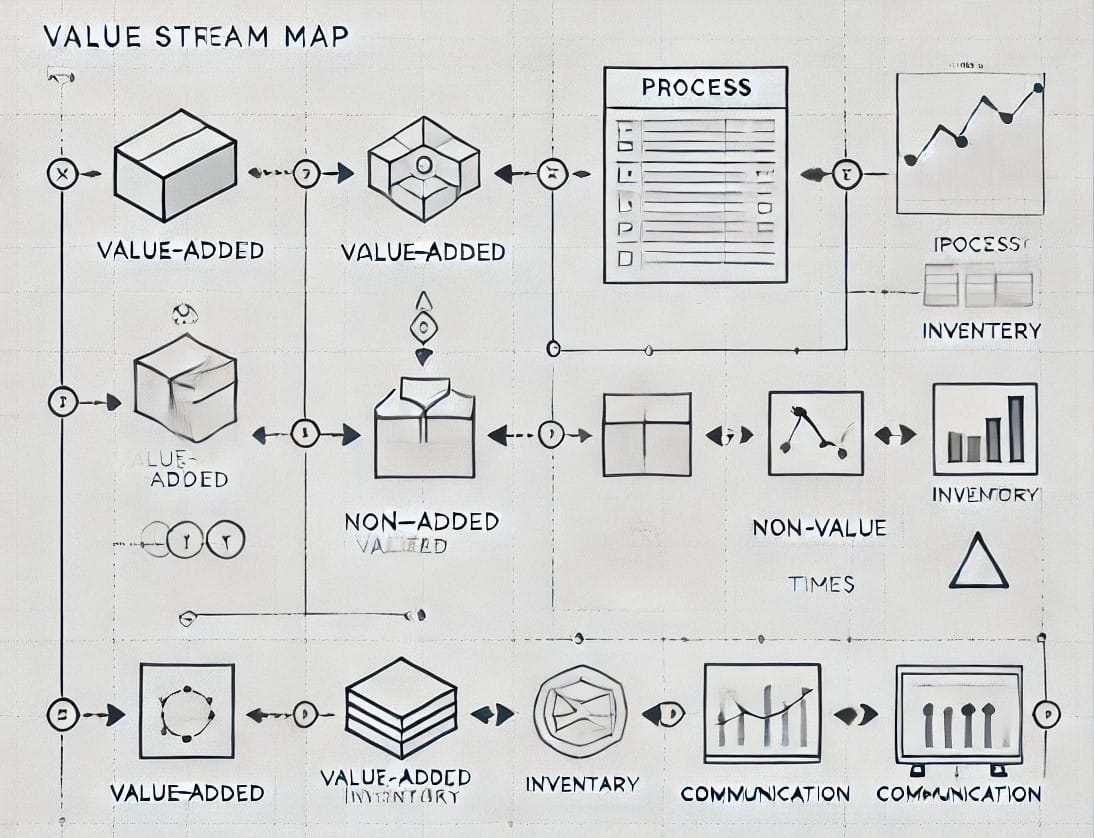
Another optimization method, that requires more practical involvement is plant layout optimization. Design the floor layout to minimize travel distance and unnecessary movements. Group related tasks and machines to streamline production flow and reduce time spent moving items between stations. This is the most straightforward way to minimize Transportation waste.
Monitor and track KPIs
To understand the current landscape and scale of challenges at a production line or the whole, it is prudent to track KPIs (key performance indicators). For example, it is possible to track overall equipment effectiveness (OEE), cycle time, first-pass yield, and downtime. This can be done manually when the production crew tracks downtime, how long the maintenance crew worked on fixing the problems, the number of finished goods produced in one shift, and so on.
However, there is an option to acquire capital expenses (CAPEX) money to implement digital/IoT solutions, which will definitely streamline the process. There are various turnkey solutions available in the market, from data loggers for various PLCs out there to stand-alone kits with sensors tracking the required KPIs. In most of the cases those off-the-shelves systems have a web-server that has dashboard. It helps to display real-time data on production status, allowing managers to identify and address issues quickly. Also, it is likely they have a historical data log, which will enable you to check the same KPI within a different time period.
Also, on the topic of maintenance, it is crucial to explore an option of proper preventative maintenance. Schedule regular maintenance checks to prevent unexpected equipment failures. It is much easier to plan and schedule production around planned shutdowns or checks than to work around an expected production line failure.
Keep learning
Also, if it is possible and allowed by local/company regulations, it can be beneficial to train machine operators to conduct basic maintenance tasks, allowing them to spot potential issues early.
Multiple organizational changes, such as cross-training, can also significantly improve the operations of any manufacturing facility. Train workers to handle various roles to increase workforce flexibility and reduce downtime due to absenteeism or workflow disruptions. Continuous training and development should also be provided to keep employees skilled in the latest technologies and methods.
"So, what is at the end?"
As you can see, multiple ways exist to optimize a production facility. In most cases, there is no right or wrong approach; it is more about finding the best strategy for your situation. It is always easier to start with more minor changes, usually related to procedures and paperwork, due to their low implementation cost. After evaluating their efficiency, more expensive (usually capital projects) approaches can be implemented.